Advanced Electric Glider Design (Capstone Project)
View our project demo video here!
For my mechanical engineering senior design capstone project, my team and I were tasked with improving the flight capabilities of a high-performing RC Electric Glider (the eSky Albatross) via rigorous aircraft performance analysis and thorough flight test. Our client, Dr. Michimasa Fujino (founder/former CEO of Honda Aircraft Company), was looking to challenge us with a complex aircraft development project while sharing his invaluable insights gained from a seasoned career of novel aircraft design and testing. I was thrilled to have a project so directly relevant to my aerospace interests with such a prominent client.
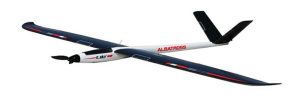
eSky Albatross Electric Glider (2.8m wingspan)
Early in the project timeline, our team settled on our primary design goals to improve the flight capabilities of the aircraft: 1) install a custom landing gear system to allow for self-powered takeoff/asphalt runway landings, and 2) modify the aircraft to improve glide performance such that the landing gear would have a net-zero glide performance impact. Essentially, the team was to design a landing gear system that would not reduce overall glide performance. We would demonstrate the final flight capabilities with disciplined flight testing in the Duke Forest.
The team of six engineers broke down into “subteams”: Aerodynamics, Structures, and Flight Test. I was to lead the Flight Test subteam, responsible for all flight-related tasks regarding the aircraft, as well as the planning and execution of flight testing in the Duke Forest. This involved:
- Developing flight test plans and procedures to achieve desired test points and demonstrate performance
- Designing a flight test instrumentation system to collect reliable data for performance analysis
- Preparing aircraft for flight (assembly, flight controls, wiring, etc.) and ensuring flight stability
- Performing post-flight analysis in Python
- Coordinating research approvals with the Duke Forest and Flight Clearances with the FAA
- Serving as Test Pilot for all flight tests (Remote Pilot in Command)
As the designated “Test Pilot” for our flight tests, I also had to earn my FAA Part 107 Remote Pilot License (sUAS), which was made easier by the fact that I already had my Private Pilot License. However, this was a fun challenge that broadened my flying experience.
The design process involved extensive Finite Element Analysis (FEA) to design a structurally sufficient landing gear, Computational Fluid Dynamics (CFD) to design effective winglets, and significant airframe modifications to make the aircraft lighter/more efficient (improving the Lift/Drag ratio and thus glide performance).
- Landing Gear FEA
- Winglet CFD
The final design incorporated modular winglets to improve aerodynamic performance, a strong but lightweight modular landing gear, a redesigned lightweight wing spar, and modifications allowing for easy implementation of flight test instrumentation:
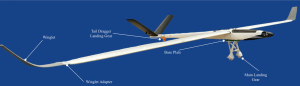
Final modified aircraft diagram
For flight test instrumentation, I designed a system that utilized a repurposed sounding rocket flight computer to sense and record rocket altitude along with GPS position and groundspeed. This allowed us to analyze the glide ratio and sink rate of the aircraft for each flight trial. Comparing glide profiles with different flight configurations (i.e. winglets, no winglets, etc.) allowed the team to understand the impact of each modification on flight performance. I also designed a system to provide in-flight telemetry via the RC transmitter/receiver to display real-time altitude information. This utilized an additional pressure-based altimeter and allowed me (as test pilot) to precisely achieve desired flight conditions for specific test points. In addition to glide performance, the team could export each flight profile to Google Earth to visualize each flight test trial and more effectively analyze data.
- Flight computer attachment
- Live altitude telemetry data
The resulting data were extremely promising, with the modified aircraft demonstrating an over 20% improvement in glide performance with the landing gear installed when compared to baseline configuration glide data! The glider was able to consistently take off under its own power on our plywood “runway”, providing additional capability with the landing gear. Some sample flight test trials from our aircraft’s development can be viewed here. Sample data produced with our flight test instrumentation is also presented below.
- Sample glide data (flight test)
- Google Earth flight data visualization
As my Senior Design Capstone Project, this was the culmination of four years of engineering design, aircraft development, and flight test experience gained from Duke, Lockheed Martin, and a lifetime passion for aviation. It was a fantastic introduction to the complex field of early-stage aircraft development and the exciting world of RC Airplanes (a newfound hobby of mine). I am grateful for our team who spent many early mornings flying in the Duke Forest, our client, Dr. Michimasa Fujino, for his indispensable insights throughout the project, and our instructor, Dr. Linda Franzoni, for her support throughout the year.
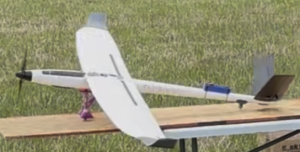
Final modified aircraft